Rostec increases service life of gas turbine engines for long-range aircraft
New Delhi, May 17
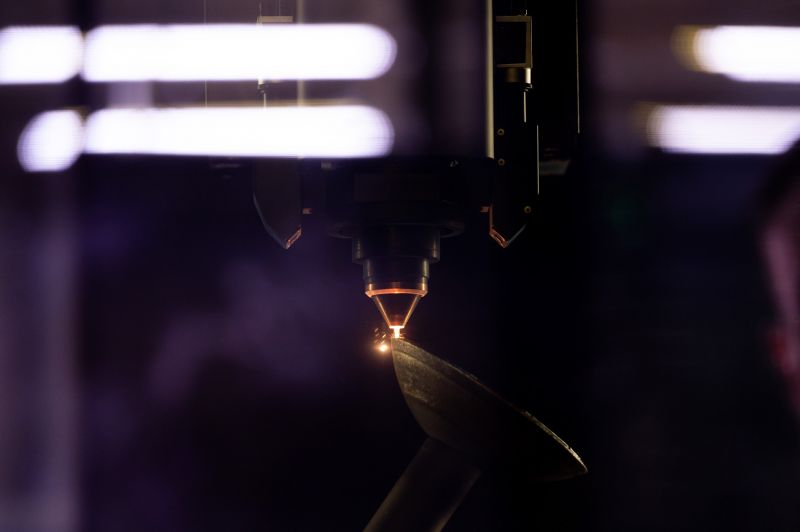
UEC-Kuznetsov, a Samara-based enterprise of Rostec’s United Engine Corporation, is improving product quality by introducing robotic equipment for applying special hardening coatings.
UEC-Kuznetsov has commissioned a robotic plasma spraying unit that automatically applies refractory and hardening coatings on engine parts, ensuring absolute repeatability and high quality.
“The new program-controlled equipment meets modern environmental standards. The industrial robot will increase the service life of all types of gas turbine engines, including the 02-series NK-32 engines used on the Tu-160 strategic missile carrier aircraft,” a representative of Rostec State Corporation’s aviation cluster said.
To increase production throughput, the robotic system has two working areas. In one of them, specialized ceramic coatings are applied to small size parts – first and second stage compressor blades and turbine nozzle sections. With this solution, it is possible to apply coatings on 12 products in a sequence within a single work cycle. The other working area features a special retractable chamber to process large-sized titanium ring blanks up to 1.5 meters in diameter.
“All equipment installed at the UEC-Kuznetsov new production facilities is high-tech and efficient. The robotic plasma spraying facility will process compressor and turbine parts for gas turbine engines not only for the United Engine Corporation’s enterprises: the equipment can be widely used as part of import substitution programs in the interests of the domestic industry,” said Alexei Sobolev, Deputy General Director, Managing Director of UEC-Kuznetsov PJSC.
Currently, the robotic system covers production demand by processing up to 100 ring parts per month in a two-shift operation. If necessary, the capacity of the equipment can be increased to 300 pieces of large-sized parts and up to 1,000 pieces of small-sized parts.
The robotic plasmatron operates using a current of up to 1,000 amperes while feeding gases (nitrogen and argon) and metal powder for sputtering. The equipment is able to apply coatings from 0.1 mm to 3.5 mm thick. Modern control systems ensure stability of the work process during non-stop round-the-clock operation. The site is equipped with the latest exhaust ventilation units with filters that prevent the ingress of metal dust into the atmosphere, and the soundproof coating inside the cabin completely eliminates the noise impact to ensure comfortable working conditions and compliance with accepted technical standards. The unit is manned by two operators.